ElecronicsV2: Arduino for Automotive DIY Projects
Table of Contents
Overview
In an era, where the automotive sector is at its prime and everyone desires to make their career advancements in the Automotive field, there is a need for a Microcontroller based development board that is of automotive grade, with automotive capabilities to do hands-on learning and gain knowledge on automotive skill sets. And in such a world, ElecronicsV2 boards make a grand entrance.
ElecronicsV2 is a development Board based on NXP Semiconductor S32K144 MCU. The development board has a rich set of onboard features and interfaces to make Automotive DIY projects. It is powered with S32K144 MCU, which is based on ARM Cortex M4 Core with Automotive peripherals like CAN, LIN, FlexIO, SAE-J2602, Half HSM, and advanced Timer peripheral.
ElecronicsV2 is not just a development board for Automotive, but it is also a prime candidate for students, working professionals, and hobbyists to learn embedded projects and learning in an industrial Microcontroller out of Arduino and ESP environment. ElecronicsV2 is based on the S32K144 Microcontroller.
S32K144 MCU is part of the S32 family of microcontrollers, for which NXP semiconductors provide a dedicated IDE for embedded software development and SDK for embedded application development. What makes the S32K144 apart, is its availability of SDK with Autosar standard!! Students and working professionals can do Autosar-based and hands-on learning using the Autosar MCAL SDK. All of this is possible/done via the ElecronicsV2 board.
Elecronics V2 Development Board
Elecronics V2: is a development board that is designed based on NXP Semiconductors S32K144 MCU by Gettobyte Community.
ElecronicsV2 is a breadboard-compatible board, which has all Input/Output pins exposed via male headers and can be expanded by embedding it into the breadboard for easy use and development. S32K144 microcontroller can be used for various industrial projects like Automotive, Industrial Automation, consumer electronics, and IoT. This board is cost-effective as compared to the original evaluation board of S32K144.
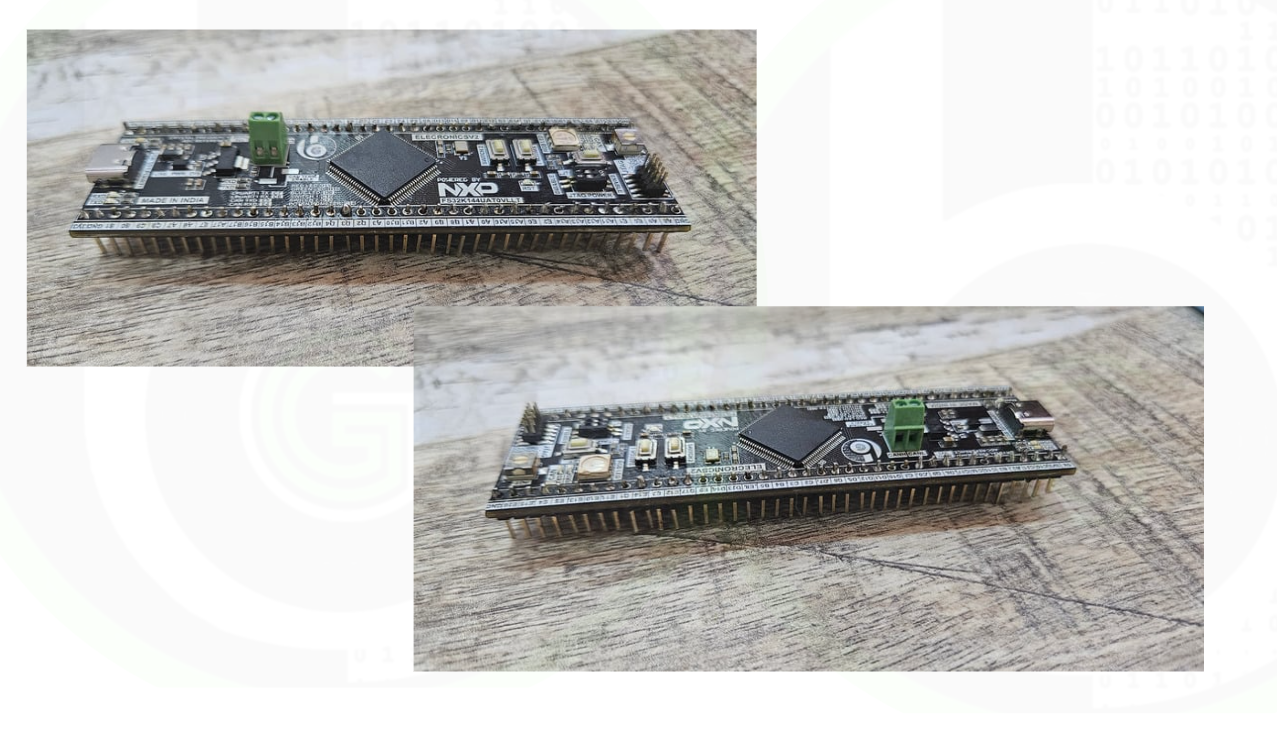
Documentation on ElecronicsV2 Board: User Manual of ElecronicsV2 Board
Getting Started with ElecronicsV2 Board: Getting started with ElecronicsV2 Board
…………………………………..
The major challenge people face is a lack of resources or scattered content to learn and do hands-on such Industrial microcontrollers. For learning the Embedded basics and firmware development on this board, viewers can refer to the tutorial blog series on the S32K144 microcontroller. Refer to this link for more info.
Features of ElecronicsV2 Development Board
ElecronicsV1 is breadboard compatible development based on NXP Semiconductors S32K144 MCU. Which has following features:

Their are 2 Best Things about the design of the ElecronicsV2 Board:
- First is 2*40 male header pins, which exposes all the pins of the Microcontroller and it can be easily connected to a number of sensor/modules with neat and clean connections
- Another thing is the silkscreen present on the board. On the ElecronicsV2 you can see there is pin labeling for all the features present on the board, which makes it easy for users to do development on the board, instead of seeing pinouts/schematics again and again.
Pinout of ElecronicsV2
About S32K144 MCU
Refer to this blog, to know indepth features and specs of the S32K144 MCU:
Reasons for starting your journey with S32K144 MCU as students/hobbyiest
- The most important reason for selecting this microcontroller is it has Software stack/drivers for S32K144 MCU with Autosar complaint MCAL Layer, which will help students learn about Autosar at the college level using ElecronicsV1 by making DIY projects just like on Arduino. Autosar is one of the highly demanded skills set in embedded and automotive industry.
- S32K144 MCU has many Automotive communication protocols like: CAN, LIN, FlexIO, Motor control-based TIMER Peripheral, CSEc Hardware Security Module to implement Cryptography Application. So using this board will give students understanding and hands-on industrial level knowledge of automotive/embedded field.
- Based on ARM Cortex M4 processor running at 112MHz, students can explore and learn about ARM technology by doing hands-on via this controller and using its IDE: S32DS.
Debugger/Programmer
The board doesn’t have on-board debugger, so it has to be programmed using external debugger like: J-Link Debuggers or PEmicro OpenSDA debugger.
Original Jlink debugger and PEmicro debugger comes very expensive, so best and reliable alternate to those debuggers i to buy JLink V9 Debugger Emulator – ARM MCU Development Tool, which comes at a cost of 2.5K around and using this debugger you can debug any ARM cortex M3/M4 chip. More details and how to use this debugger is here.
JlinkV9 Debugger is Chinese clone of the original Jlink Base Debugger which is best to use by students/hobbyists and affordable too.
Viewers can buy the debugger from here: Buy JLink V9 Debugger Emulator – ARM MCU Development Tool – KTRON India.
It comes at a cost of 2.5K around. Buying this debugger once and then it can be used with any ARM Cortex M based Microcontroller.
Other alternative for debuggers:
Target Audeince for the board
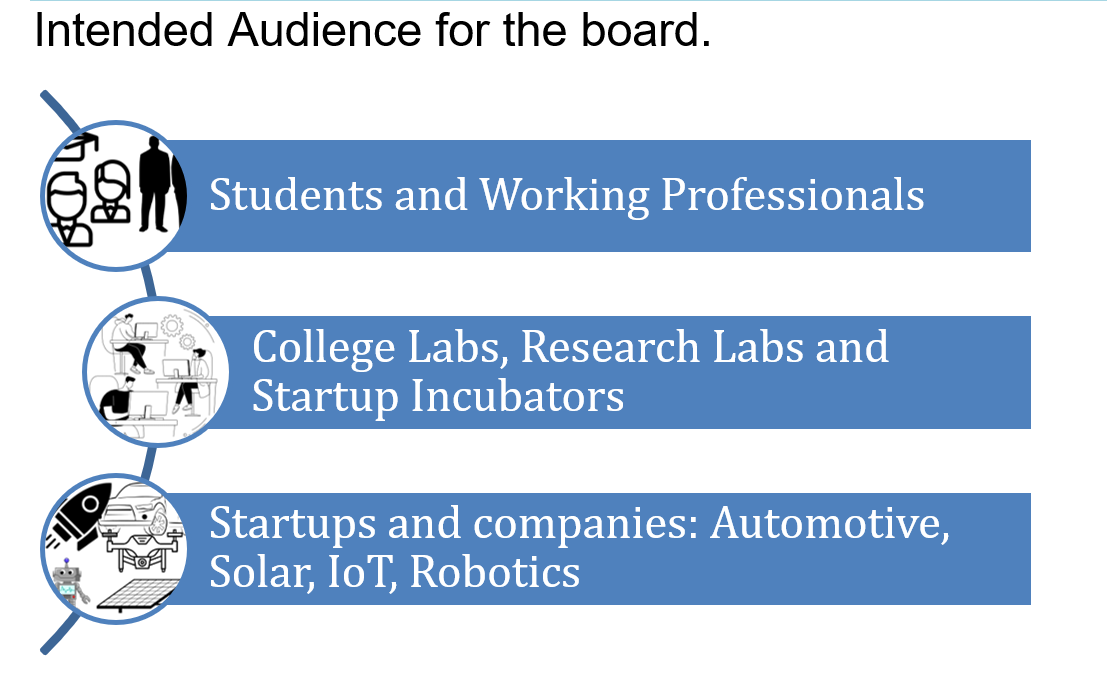
The board can be used by variety of audience and applications as follows:
- It can be used by students and practise enginners for learning Embedded systems on Industrial Microcontrollers like that of NXP Semiconductors to come out of Arduino and ESP environment and making DIY projects for different Industries, giving them industrial exposure and skillsets. Thus, this microcontroller is perfect start for students to get hand-on exposure on industrial technologies.
- Not only for DIY projects but this board can be used for fast prototyping and development by automotive/EV based startups/companies for their product development. As S32K144 MCU is ARM cortex M4 based and has rich set of peripherals with automotive certified standards for developing products for body & control, powertrain and electrification domains of the car.
Buy the board
The board is priced at INR 4,999(Excluding GST and Shipping Charges).
For college students, ElecronicsV2 is of 2,999. For students, there is a discount of INR 2000. They have to submit their student ID and government ID, after the verification from our end, their order will be processed.
The Kit will include, Jlink V9 debug Users can buy from above link:
- One ElecronicsV2 Development Board
- JTAG-SWD Debug Adaptor
- 10 Pin JTAG debug connecting wire
Getting Started with Board
For using the S32K144 MCU, NXP semiconductors provides S32Design Studio IDE and S32K1 Software Package. S32K1 Software package has all the peripheral drivers, example codes, middleware stacks for starting development/learning on S32K144 MCU. on Refer above video to get started with ElectronicsV1 board and how to setup S32K144 SDK.
Further viewers can refer to blog series on S32K144 MCU, to do hands-on learning on all of its peripherals and then do sensor-module/DIY Projects interfacing with using ElecronicsV1 board.
Chronological order to start with this board:
Kunal Gupta
Edge AI ToolKit: EiQ AI SDK
Introduction to EiQ In previous blogs, we’ve discussed in depth Edge AI, its features, advantages, and future scopes. Implementation of
What is Cyber Security Management System in AIS-189?
In the context of AIS-189, the Cybersecurity Management System (CSMS) is a mandatory framework that all automotive manufacturers (OEMs) and
Project Ideas for Edge AI in Industrial Automation: Industrial Sensor and Indicator’s
🏭 Project Idea 1: AI-Based Production Line Blockage and Jam Detection Using Proximity & IR Sensors 🎯 Goal: To build
Project Ideas for Edge AI in Power/Energy Industry: Smart Meter and Smart Grid
📊 Project Idea 1: AI-Based Non-Intrusive Load Monitoring (NILM) in Smart Energy Meters 🎯 Goal: To develop an Edge AI
Project Ideas for Edge AI in Automotive Industry: BMS + EV Charging
🔋 Project Idea 1: Edge AI-Based Battery SoH Estimation and Failure Prediction System 🎯 Goal: To build a real-time SoH
Usecases of Edge AI Technology?
So yes — Edge AI is not limited to just detection and prediction. When you look at it from a
Add Your Heading Text Here
Author