What is OLED Technology?
OVERVIEW
Nowadays we see oled display being used everywhere be it the phones , TVs , laptops or PCs , smartwatches . They sure are better than old chunky CRT TV displays that were bulky and didn’t deliver the desired picture quality , with the introduction of the LCD and backlight LEDs the things sure got better with the chunkiness of the display gone but the picture quality still wasn’t what one desired of but with the release of the OLED display all these problems became a thing of past. OLED or organic light emitting diode were invented in 1987 by Ching Tang and Steven Van Slyke from Kodak but it was until 2004 when SONY released a OLED TV. In fact in CES 2019 , there were some innovative inventions that were released in the OLED domain with the companies trying to come up with foldable display and some exceptional picture quality.
TYPES OF OLED
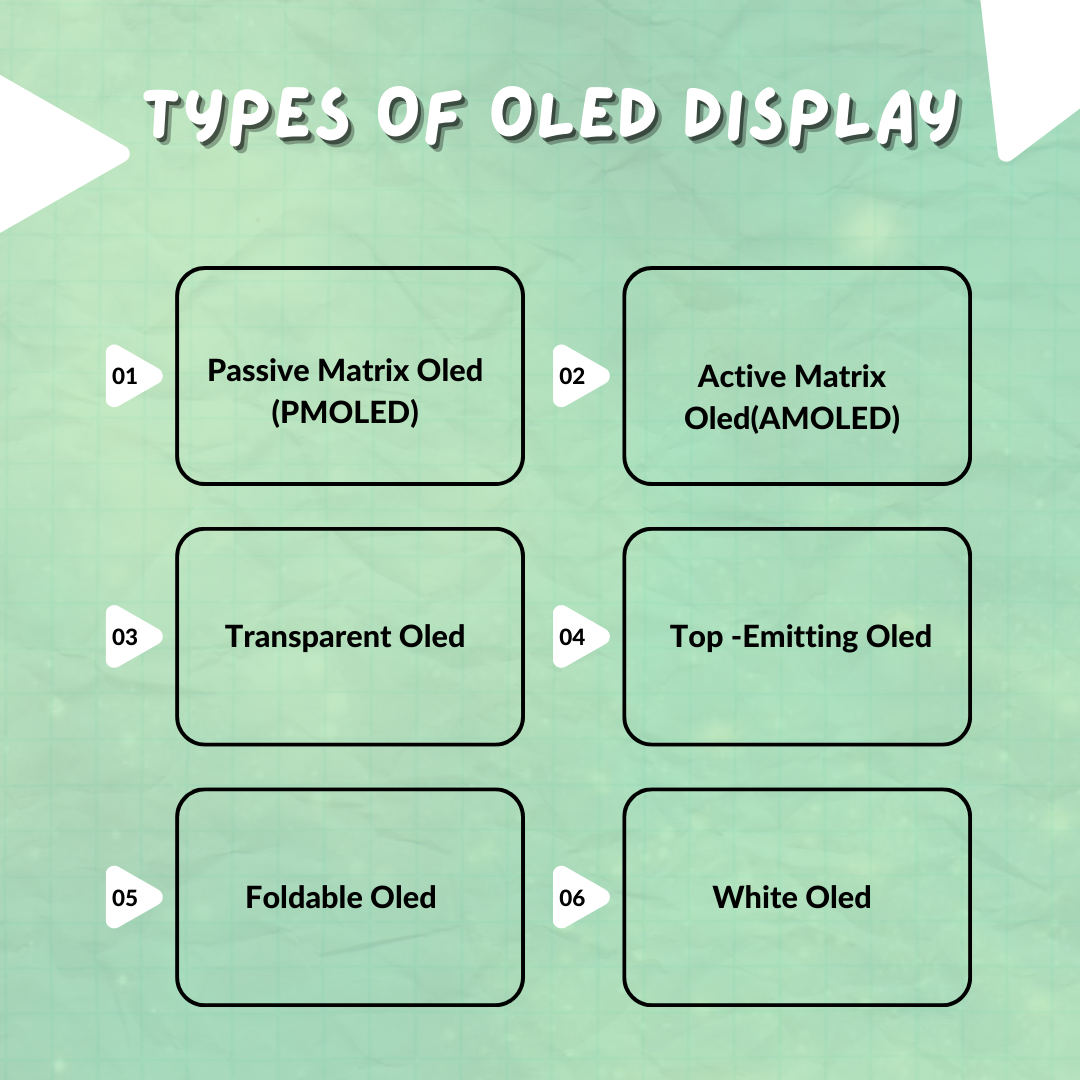
Passive Matrix Oled (PMOLED)
Pmoleds have strips of cathode , anode and organic layer. The anode strips are perpendicular to cathode strips it is their intersection that makes a pixel . External circuitry applies current to the cathode and anode strips to decide which pixel to light up. They are used in MP3 players , cell phones etc.
Active Matrix Oled(AMOLED)
Amoleds have full layer of anode and cathode and organic molecules . The anode layer overlaps the TFT matrix array . The TFT array is the matrix circuitry that decides which pixel gets turned on form the image. Since they consume less electricity they are used in TV screens , BillBoards, Computer Monitors.
Transparent Oled
A Transparent Oled has all the components cathode, anode, substrate transparent and when off the display is 85 percent transparent. When switched ON the display allows the transfer of light in both the directions.
Top Emitting Oled
The Top Emitting Oled is have substrate that is either opaque or transparent . They are best suited for active matrix design . They are used in smartcards
Foldable Oled
They are substrate that made of flexible metallic foil , plastic . They are durable and are easier to replace in case of damage . They are used in smart clothing , GPS receivers , IC computers.
White Oled
They are made of white light that is more uniform and energy efficient rather than fluorescent lights. They posses true color of incandescent lights
BESIDES THESE OLEDS ARE ALSO CATEGORIZED ON THE BASIS OF
- Monochrome Blue
- Monochrome white
- Yellow Colour
- 3 Pins (supports only I2C)
- 7 Pins(supports both I2C and SPI)
- SSD1306
- SSD1331
- 0.91 inch(128×32)
- 0.96 inch(128×64)
HOW OLEDs WORKS
- Both the LCD and OLED have similar display mechanism . The difference lies in the fact that OLED has the smallest display unit made of pixels that are usually 0.3mm x 0.3mm . Inside each pixel they are 3 different type of color filters . When the size of the color filter is reduced then human eye losses its ability to view each color individually and sees them as a mixture. Next each pixel is converted into digital form for future reproduction of the image.
- Earlier the image reproduction was done using backlight white , colour filters, glass , diffuser . When the light would glow each color filter would light up too. Behind the filters a polarizer lcd sheet is used which reproduces the image , the problem with this was the black colour produced wasn’t exactly black due to the back light being ON constantly .
- This issue was rectified using tiny light sources for each pixel due to which organic led was used . If we apply positive voltage to the anode termina the electrons would combine with the holes in the LUMO layer producing light. Work is also being done to remove the need for light source and add doping material in the emission layer which will release light of the certain color due to the energy difference in the conduction and valence layer corresponding to their wavelengths
FIG -1 SIZE OF A SINGLE PIXEL
FIG-2 RGB COLOR FILTERS INSIDE A PIXEL
FIG -3 CONVERTING EACH COLOR INTO BINARY
FIG -4 CROSS SECTION VIEW OF OLED
FIG-5 CHANGING THE ORIENTATION OF THE POLARIZER TO GENERATE DIFFERENT COLORS
FIG -6 ELECTRON HOLE PAIR COMBINATION TO GENERATE LIGHT
FIG – 7 DOPING OF SUBSTRATE TO GENERATE LIGHT OF VARIOUS WAVELENGTH
USE CASES OF OLED DISPLAY
-
Raspberry Pi Based SSD1306 OLED Video Player
This project uses Raspberry pi and OpenCv to display videos on the Oled display
-
ESP8266 Weather Widget
This project used ESP8266 and weather API to display real time weather conditions on the 0.96 inch display.
-
Tinyduino gamepad
The project used joystick , push buttons , arduino uno , custom designed PCB , USB module and ssd display to play games on the tiny 0.96 inch screen
-
Bluetooth Smartwatch
The project uses 0.96 display , bluetooth module , tiny arduino , lipo battery to connect to the phone and display all kinds of medical stats and time
-
Speedometer for bikes
The project uses gps module neo6m and ssd1306 display to show speed of the vehicle on the display and raise an alarm in case of overspeeding.
HOW TO CONNECT THE DISPLAY WITH THE MICROCONTROLLER
WE WILL BE COVERING THE DETAILS ON HOW TO CREATE AN EMBEDDED DRIVER FOR THE DISPLAY IN THE NEXT BLOG . IN THIS WE’LL BE COVERING A BRIEF OVERVIEW OF THE 2 METHODS THAT CAN BE USED TO COMMUNICATE WITH THE DISPLAY.
Using I2C we’ll be communicating with the microcontroller by the help of SCL the clock pin that will keep the data transfer in synchronization and SDA the bus on which the data will be communicated.The speed in this case will be less but the no of pins required for communication is less and can be shared by other displays or sensors.
In SPI we’ll be communicating with the microcontroller using the pins CLK which is the clock input to the microcontroller . MOSI is used for displaying the data sent by microcontroller , Reset pin Resets the internal buffer of the OLED driver, DC this pin is used to separate the commands such as cursor position , clear screen from the data buffer, CS chip select is used to select the SSD1306 Oled display.
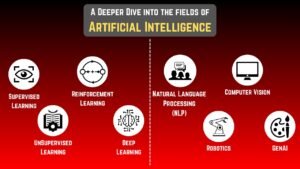
A Deeper Dive into the fields of Artificial Intelligence
So far, we’ve learned about the types of AI, Family of AI, its features and limitations. Here, in this blog,
What is Edge AI Technology?
Lorem ipsum dolor sit amet, consectetur adipiscing elit. Ut elit tellus, luctus nec ullamcorper mattis, pulvinar dapibus leo. How to
What is Artificial Intelligence (AI)? A Beginner’s guide from Gettobyte
Artificial Intelligence, or AI, one of the most commonly discussed technologies today – powering everything from voice assistants like Siri
A Deep Dive into SHE Key Slots for Automotive Microcontrollers
In the realm of automotive cybersecurity, microcontrollers must support secure storage, cryptographic operations, and boot integrity. To meet these requirements,
Autosar Technology
Before Autosar and challenges Before the development of AUTOSAR (AUTomotive Open System ARchitecture) in 2003, the automotive industry lacked a
What is Embedded Security in Embedded System’s?
🔐 Embedded Security in Automotive ECUs: A Deep Dive into Core Mechanisms Meta Description: Discover how embedded security mechanisms like
Author